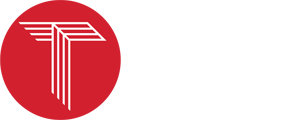
Think : Thermal : Thermal Product Solutions: First and Foremost, Committed to Safety
Posted on June 03, 2015 in Safety
Thermal Product Solutions: First and Foremost, Committed to Safety
At TPS, the safety of our employees and customers is our top priority. Although our Gruenberg, Tenney, Blue M, Lindberg MPH, and Wisconsin Oven brands are known for their robust construction, superior quality, and performance – all virtues that can be seen, it’s what you can’t see that is the foundation of every product we make: our commitment to safety.
That commitment begins first with the culture of safety that we have established for the employees, equipment, policies and processes in our workplaces. We’ve created this culture not just because we want to avoid lost time caused by workplace injuries or fines resulting from safety violations. Although those goals are important and admirable, they’re not the underlying factor. TPS is strongly committed to safety, because it’s essential for the health and wellbeing of our employees, customers, and every end user of our products, for the lifespan of each of those products.
TPS’s culture of safety extends to our supply chain, design and engineering, product development, manufacturing, testing, and customer training. As a manufacturer of products that dry, heat treat, cure, anneal, melt, sterilize, hot stamp, and press harden materials and other products and subject them to rigorous conditions such as extreme heat, humidity, shock, vibration, vacuum, and altitude, it’s vital that we get safety right. And nowhere is this more important than for our ovens, chambers, rooms, and furnaces that are used in the testing or treating of products such as solvents, paints, batteries, and other materials that are flammable, combustible, and are at risk for explosion.
As a leading manufacturer of industrial ovens, environmental test chambers and rooms, and lab furnaces and crucibles, TPS requires all of our employees to wear personal-protective equipment, such as safety glasses, welding shields, and gloves, as well as respirators and flame-resistant, arc-flash suits whenever necessary. We also provide mandatory, monthly, safety training on a variety of topics to ensure that our employees have the knowledge and resources necessary to perform their jobs safely and to protect themselves and their coworkers from workplace injury. Each topic is covered at least once annually. Our timely, comprehensive training program and employees’ understanding of the importance of compliance with safety protocols have resulted in an extremely low rate of workplace injuries.
To protect customers and other end users of our products, our design engineers integrate numerous, standard safety features, such as over-temperature protection or safety shut-off switches, into each oven, chamber, or furnace we build. Standard safety features correspond with each product’s configuration and intended use. For example, gas-fired ovens require additional safety features beyond those needed for electric-powered ovens. Both are designed with air-flow safety switches that turn off the equipment in the event of a blower failure. However, gas-fired ovens also include flame-monitoring safety packages and interlocks on the gas train to ensure proper pressure of incoming gas. Likewise, backup contactors on electric-powered ovens allow the operator to disconnect power to the heating elements in cases where the main device malfunctions and fuses together.
Working to specific customer requirements, our engineering design solutions teams can enhance or modify standard safety features or add fully customized safety features, such as inert atmospheres, rapid-purge systems, solvent monitors, gas analyzers, automatic door locks, pressure-relief ports, product-monitoring thermocouples, intrinsic safety barriers, rapid cryogenic cooling systems, fire-suppression systems, Class “A” ventilation systems, and other specialized safety features to meet the customer’s specific applications.
Finally, TPS also prioritizes safety when developing our product-user manuals and other customer information as well as during customer training. We know problems can arise if users don’t follow the manufacturer’s guidelines or heed limits of an oven’s or chamber’s load. For example, an NFPA 86 Class “A” oven that is suitable for processing flammable solvents or vapors is designed to handle a maximum amount of solvent that is present at a specific temperature. Overloading the oven with more solvents or vapors than the level for which the oven is rated would create a dangerous situation that could lead to fire or explosion.
That’s why TPS urges its customers to ensure that employees who operate our Gruenberg, Tenney, Blue M, Lindberg MPH, and Wisconsin Oven equipment are fully trained in the operation, safety, and maintenance of the equipment they operate. Adherence to manufacturer’s guidelines and a detailed preventive maintenance program are vital to maintaining the integrity and safety of the equipment.
With decades of experience in building the safest industrial ovens, environmental test chambers, and lab furnaces on the market today, we take safety seriously. That’s why the quality of the equipment we manufacture meets the highest standards of performance and safety.